When a guitar neck snaps, most players assume their instrument is destined for the trash heap. We’re here to tell you that’s not always the case. With the right tools, techniques, and a steady hand, many broken necks can be successfully repaired at home. While it’s not a job for the faint-hearted, we’ve seen countless DIY repairs that rival professional work. Let’s break down the process of bringing your beloved axe back to life.
Understanding Guitar Neck Breaks: Common Causes and Assessment
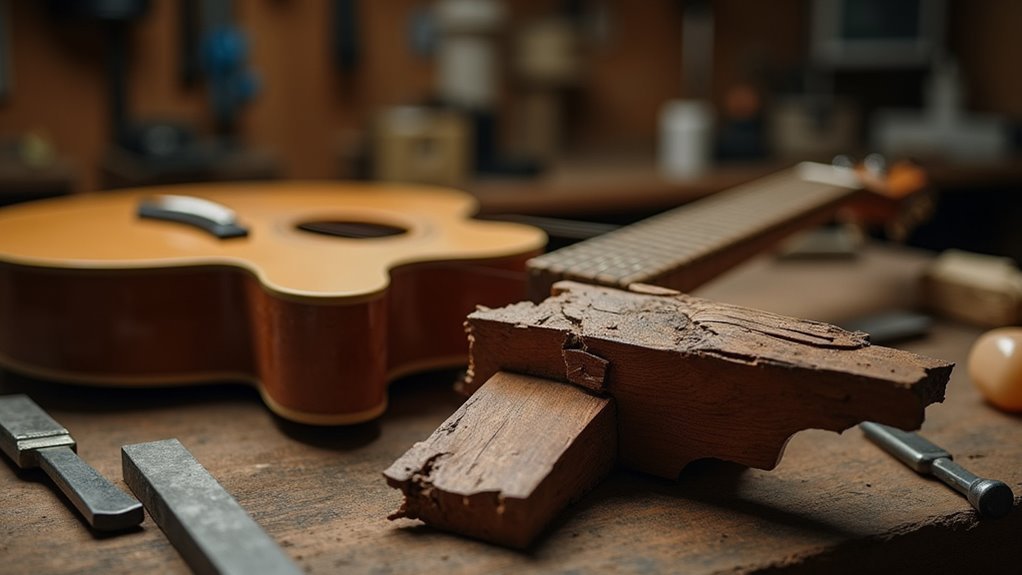
Nearly all guitar neck breaks occur at predictable stress points, and we’re going to help you spot them before disaster strikes.
The most vulnerable area? That angled headstock design you’ll find on popular models like Gibsons. It’s a notorious weak point just begging for trouble.
Here’s what we’re looking for when evaluating a broken neck: clean breaks are your best friend. They’re straightforward to fix and often result in stronger repairs than the original wood.
But if you’re dealing with multiple fractures or previous repair attempts, you’re in for a challenge.
Watch out for thin neck areas, especially around the truss rod channel. These spots are prime candidates for breaks under normal string tension.
Understanding these weak points is essential for choosing the right repair methods.
Essential Tools and Materials for Neck Repair
Before you even think about fixing that broken neck, you’ll need to gather the right arsenal of tools – and we’re not talking about your trusty hammer and duct tape.
Let’s start with the essentials: high-quality wood glue (the white stuff, not that bargain-bin adhesive), multiple clamps of varying sizes, and a fine artist’s paint brush for precise glue application.
You’ll also need a proper support structure to keep that neck perfectly aligned while the repair sets.
Don’t forget your clean-up supplies – water and paper towels are non-negotiable for managing glue mess.
Keep a box knife handy for opening containers and prep work.
And yes, grab some wood filler while you’re at it – those tiny gaps won’t fill themselves.
Preparing Your Workspace and Safety Measures

While your guitar’s been silently screaming for repair, we’ve got to set up a workspace that won’t make things worse. First, claim a sturdy workbench – your kitchen table won’t cut it. Let’s make safety non-negotiable with safety goggles and proper ventilation, especially when adhesives enter the chat. Keep that first aid kit within arm’s reach – minor cuts happen.
Must-Have | Why It Matters |
---|---|
Clean Space | Prevents lost parts |
Workbench | Stability is key |
Ventilation | Fumes are nasty |
Safety Gear | Eyes and lungs first |
Think of your workspace as mission control. It’s not just about having room to work – it’s about creating an environment where precision repairs become second nature. Organization isn’t optional; it’s your first line of defense against costly mistakes.
Step-by-Step Repair Process: From Break to Bond
Once you’ve spotted where your guitar’s taken a hit, it’s time to plunge into surgery mode.
We’ll start by examining the break and cleaning all surfaces – trust us, debris is your enemy here.
Grab your modeler’s paintbrush and apply wood glue evenly to both broken surfaces. Don’t rush this step. We’ll do a quick dry fit to guarantee perfect alignment before bringing in the clamps.
Speaking of clamps, you’ll want various sizes to maintain consistent pressure during the hours-long drying process.
After the glue’s set, we’ll tackle any excess with sandpaper for that smooth finish.
For extra peace of mind, we can route reinforcement channels and add custom blocks. These hidden heroes will strengthen your repair and help prevent future breaks. No one will ever know the difference.
Clamping Techniques and Drying Time Guidelines

When it comes to proper clamping, we’re not messing around – this step can make or break your repair job.
We’ll need both C-clamps and bar clamps to distribute pressure evenly across the break. Before you even think about reaching for those clamps, double-check your alignment. Trust us, a misaligned neck means a guitar that’ll play like a twisted pretzel.
Lock those clamps down tight, but don’t go Hulk on them. You’ll want to check them periodically during the drying time – they can loosen up as the glue sets.
Exercise restraint when tightening clamps – brute force won’t help. Monitor pressure throughout drying, as clamps may need adjustment.
Give it a full 24 hours minimum under pressure, longer if your glue manufacturer says so. Once you’ve removed the clamps, inspect your handiwork and sand down any rough spots.
No shortcuts here, folks.
Finishing Touches and Structural Reinforcement
Now that you’ve got a solid bond, it’s time for the vital finishing work that’ll make or break your repair’s durability. Let’s tackle these finishing touches systematically while ensuring structural reinforcement.
Step | Action | Purpose | Tool Needed |
---|---|---|---|
1 | Sand edges | Smooth shift | 220-grit sandpaper |
2 | Route channels | Add support | Router & bits |
3 | Insert blocks | Strengthen joint | Hardwood blocks |
4 | Match finish | Blend repair | Nitro lacquer |
After reinforcement, we’ll need to dial in the truss rod adjustment. Don’t skip this – it’s essential for proper neck relief and string action. Remember: a perfect cosmetic repair means nothing if the neck can’t handle string tension. Test thoroughly before declaring victory.
Testing and Setting Up Your Repaired Guitar
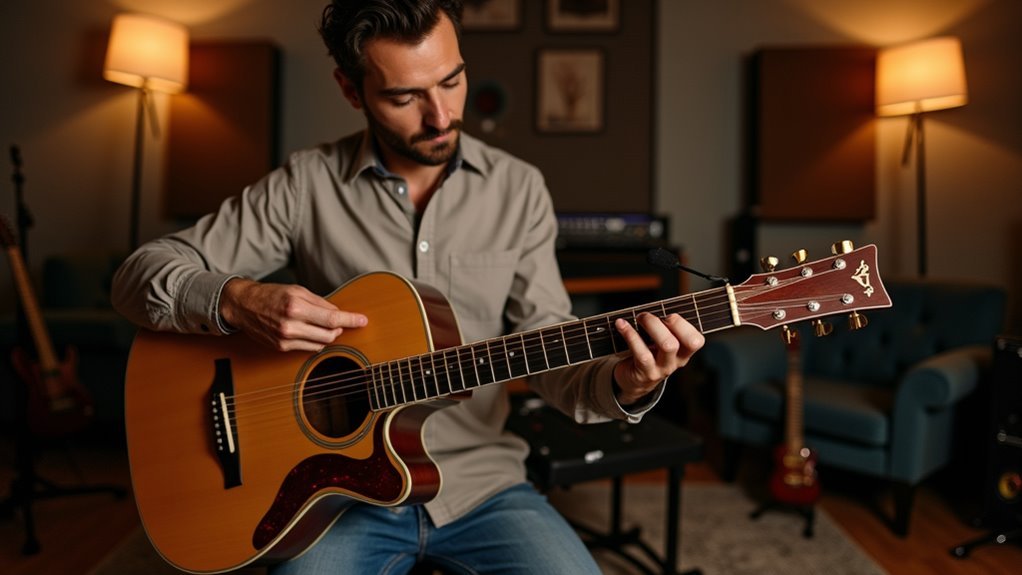
The critical moment of truth has arrived – it’s time to put your repaired guitar through its paces.
Let’s start the testing process by restringing your instrument and checking the neck’s playability under tension. We’ll assess string height, action, and alignment to guarantee everything’s centered perfectly over the fretboard.
Next, we’re diving into truss rod adjustments. This vital step fine-tunes neck curvature – too concave or convex will wreck your playing experience.
The truss rod is your precision tool – master its adjustment to achieve that perfect neck relief your playing deserves.
Run your fingers across those frets and listen for buzzing or dead spots while playing chords. They’re your early warning system for structural issues.
Don’t forget the cosmetics. That repair area needs to feel as good as it looks.
Sand and polish until the finish shifts smoothly. Your repaired neck should feel like it never broke.
Frequently Asked Questions
Is It Possible to Repair a Broken Guitar Neck?
Like mending broken bones, we can heal guitar necks through proper neck repair techniques. Whether acoustic or electric guitar neck types, DIY guitar fixes are possible with the right tools and patience.
What Is the Best Glue for a Broken Guitar Neck?
We recommend wood glue as the best option, specifically wood white glue, for its strong bond and easy application. While epoxy and cyanoacrylate can work, they’re not ideal for guitar neck repairs.
Can You Break a Guitar Neck With a Truss Rod?
Problematic, precarious truss rod adjustments can definitely damage or break a guitar neck. We must maintain proper neck stability through careful guitar maintenance to avoid catastrophic tension that compromises the wood’s structural integrity.
Do All Guitars Eventually Need a Neck Reset?
We don’t need neck resets on all guitars, but some will develop neck angle issues over time. With proper care, regular action adjustments, and minimal fret wear, many guitars avoid this repair.